Flying corrosion inspection robot for infrastructures
Responsible: Patrick Pfändler1, Karen Bodie2
1 Institute for Building Materials, ETHZ
2 Autonomous Systems Lab, ETHZ
Funding: ETH Research Grant
Collaborations: ASL (Autonomous Systems Lab) from the Department of Mechanical and Process Engineering (D-MAVT) from ETHZ

The following video shows a fast replay of the prototype of the flying robot when measuring potentials on a bridge girder:
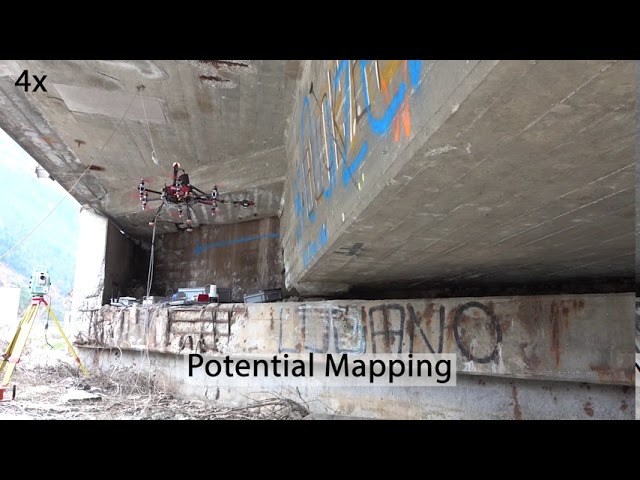
Background
The current manner of inspection of ageing concrete structures such as bridges, using non-destructive testing methods, is limited in terms of:
- Accessibility of the structure: often heavy equipment is needed for measuring personnel to access the structural members of interest (e.g. underside of a bridge).
- Efficiency and spatial resolution of manual measurements.
- Data acquisition and data analysis are decoupled as generally first the measurements are done on-site and in-depth analyses are done later in the office. This limits the extent to which adjustments during the measurement can be made, e.g. to acquire more data in “interesting areas”.
Due to these limitations, traditional inspection is laborious and costly and is thus generally not used in routine inspections, but only in cases where deterioration has already progressed to some extent. Early detection of deterioration is thus difficult.
We see a large potential in the development of flying robots that can partially or completely automate well-proven, non-destructive corrosion assessment measurements on-site, to provide a sound basis for the decision-making and maintenance planning of ageing infrastructures.
Aims and objectives
This project aims at delivering the scientific and engineering basis needed for flying corrosion inspection robots for reinforced concrete infrastructures via a collaborative research effort. We expect to deliver a fully functional prototype as well as important research contributions on all relevant challenges related to nondestructive corrosion detection and similar flying contact-based inspection tasks.
Methodology
In order to achieve the goal of delivering such a flying corrosion inspection robot numerous questions related to the fields of robotic and civil engineering challenges needs to be addressed. This includes a novel design and building of an omnidirectional robot that is able to exert controlled forces to a structure.
The flying robot will be able to fly autonomously precisely to hardly accessible structural members to conduct the electrical and electrochemical measurements. The potential mapping is a well-proven non-destructive measurement to locate on-going corrosion through the concrete cover.
The omnidirectional robot is equipped with a tailor-made reference electrode for the potential mapping as well as a probe for electrical concrete resistance measurements, which is optimized to fit the weight and geometry restrictions of the flying robot. Our approach also combines the visual-based assessment (cracks, honeycombs, etc.) with the contact-based NDT-sensor readings to locate corrosion damages with higher accuracy and efficiency compared to the traditional approach.
Early-stage detection of degradation can lead to considerable savings of maintenance and repair costs.
The following figure shows that the flying inspection robot measures similar potentials on a lab-sized reinforced concrete sample compared to manual measurements conducted before and after the flights.

Videos
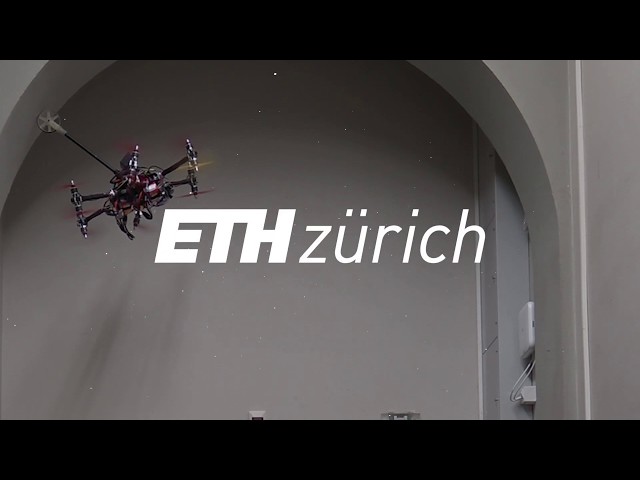
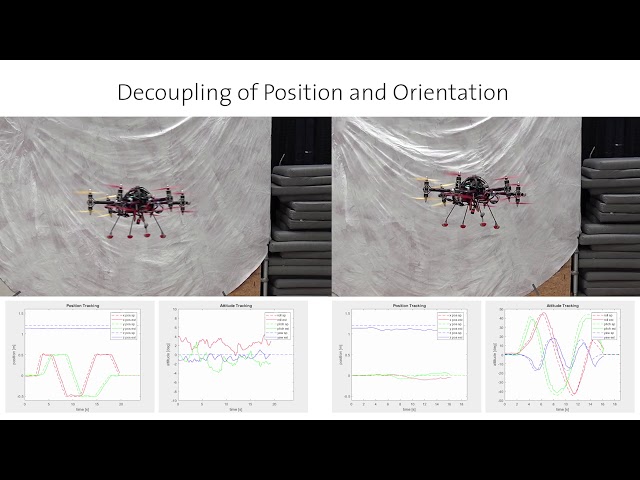
Publications
- Pfändler, P., Bodie, K., Angst, U., & Siegwart, R. (2019). Flying corrosion inspection robot for corrosion monitoring of civil structures – First results. SMAR 2019 - Fifth Conference on Smart Monitoring, Assessment and Rehabilitation of Civil Structures - Program, We.4.A.6. external page https://doi.org/10.3929/ETHZ-B-000365572
- Bodie, K., Brunner, M., Pantic, M., Walser, S., Pfändler, P., Angst, U., … Nieto, J. (2019, May 9). An Omnidirectional Aerial Manipulation Platform for Contact-Based Inspection. external page https://doi.org/10.15607/rss.2019.xv.019
- Bodie, K., Brunner, M., Pantic, M., Walser, S., Pfändler, P., Angst, U., … Nieto, J. (2020). Active Interaction Force Control for Omnidirectional Aerial Contact-Based Inspection. ArXiv Preprint ArXiv:2003.09516.
- Bodie, K., Taylor, Z., Kamel, M., & Siegwart, R. (2020). Towards Efficient Full Pose Omnidirectionality with Overactuated MAVs. In J. Xiao, T. Kröger, & O. Khatib (Eds.), Proceedings of the 2018 International Symposium on Experimental Robotics (pp. 85–95). Cham: Springer International Publishing.