New mobile underground inspection technology device for retaining walls
Responsible: Lukas Bircher, Patrick Pfändler
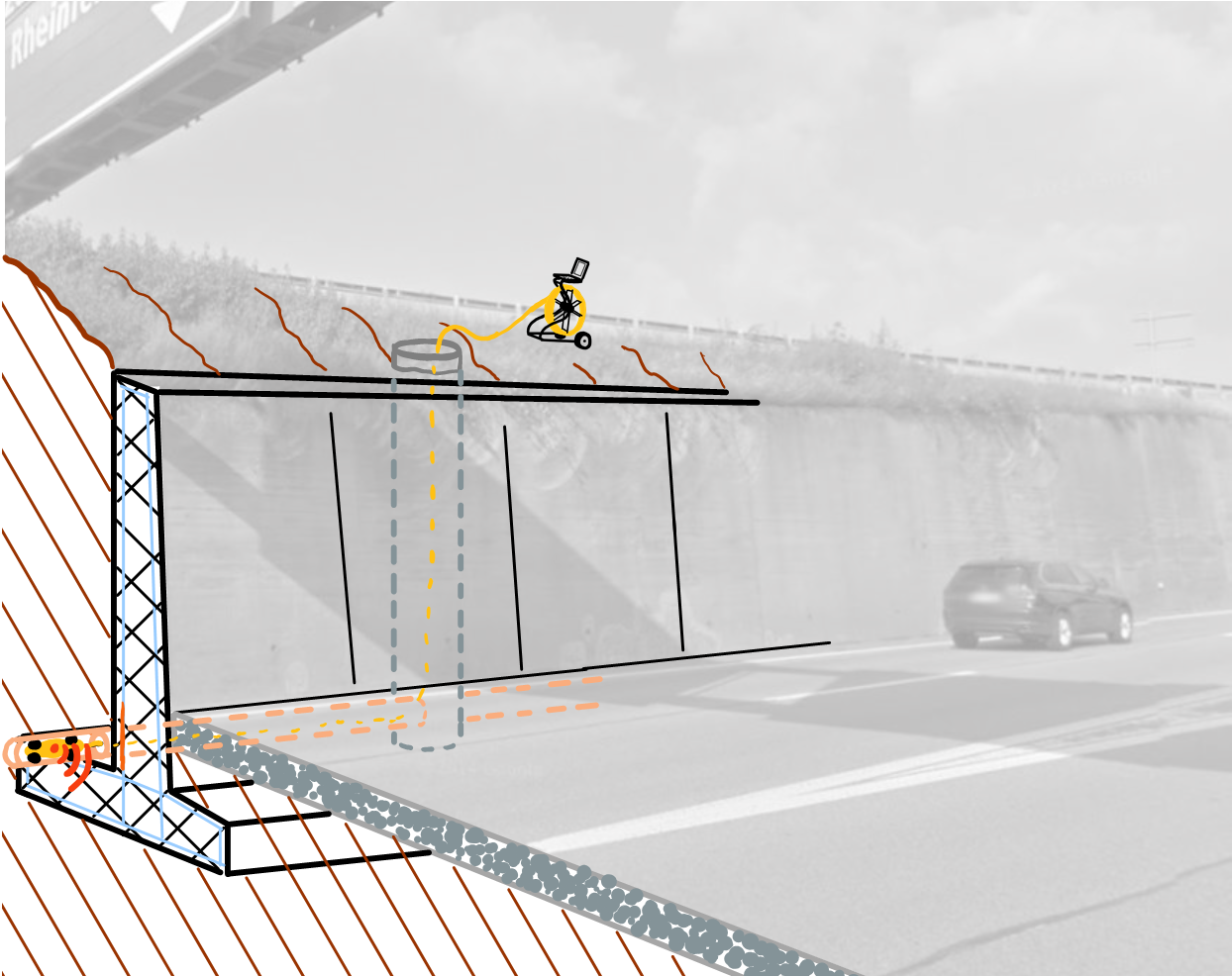
Background
The ageing of our infrastructure will inevitably entail an increased number of inspections in the next decades. This is particularly a problem for buried structures with limited accessibility for a reliable inspection, such as retaining walls. It is well documented that the reinforcing steel embedded in the concrete at the backside of retaining walls (side in contact with the ground) close to the foundation, can corrode and increases the risk of a collapse. This presents a twofold problem: First, the inspection of this part of the structure is virtually impossible, which leads to expensive repair and strengthening construction works without direct evidence for its need. Second, corrosion at this location in the structure is the most critical and can cause sudden failure of the wall. Thus, if undetected and if no maintenance is done, the public is exposed to an unknown risk.
Today, therefore destructive technologies, such as core drilling or excavations, are commonly used for the inspection of retaining walls. These methods for the detection of steel corrosion have severe drawbacks: due to their high costs and destructive nature, they only allow for “local snapshots” of the structure’s condition. Destructive inspections lead to permanent changes in the structures and can therefore only be repeated a few times. The lack of continuous information along the complete length of retaining walls makes it impossible to determine whether the structure can be used safely or needs immediate repair.
Aims and objectives
The key idea is to deliver an innovative corrosion inspection technique, as a solution to tackle the important problem of guaranteeing the safety of traffic infrastructures lines near cantilever retaining walls. The approach consists of a specifically developed device that can move within existing drainage pipes in the backfill of the retaining walls to detect the corrosion in the structure next to the pipe.
Advantages:
- The ability to yield an assessment of the corrosion condition over the entire length of a structure, as opposed to the very local information that can currently be obtained. Since the corrosion damage in a structure is expected to occur locally, state-of-the-art methods can only detect these damages with very low probability. Our device can detect such weak points because it carries out well-established electrochemical measurements over the entire length of the retaining wall. This enables a complete condition survey of the critical area and thus considerably increases safety due to more information.
- Considerably reduced costs for inspection and maintenance as well as benefit for the environment due to reduced consumption of energy and raw materials (avoiding unnecessary repairs). Our new, precise condition assessment has a great cost-saving potential, as it enables targeted preventive maintenance and local repairs, and thereby prevents expensive large-scale repairs.
- The inspection is almost non-destructive.
The method yielded promising results in the lab and a field trial but needs further development for the application on construction sites and thus for a proof of concept.
Methodology
The laboratory method needs to be further developed to provide a robust and reproducible technology that produces reliable results in harsh environments as well as on large objects.
The validation of the technology will be tested on a structure in collaboration with infrastructure operators. To achieve this, it is mainly needed to develop the hardware to transfer the current 3D printed prototypes into a robust inspection device.